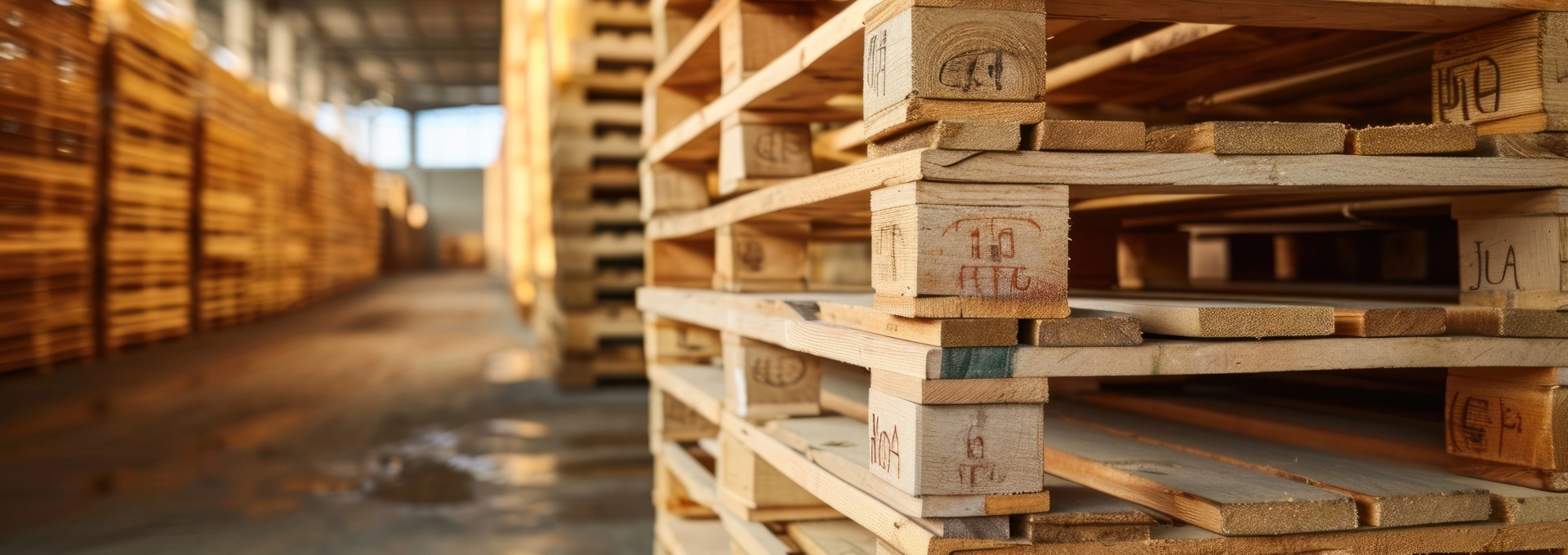
Le choix d'une solution de stockage de palette à Paris adaptée aide à augmenter l'efficacité opérationnelle et la rentabilité de votre entrepôt. Avec l'évolution constante des technologies logistiques et l'augmentation des volumes de marchandises à gérer, il convient de bien comprendre les différentes options disponibles et leurs implications. Que vous gériez un petit entrepôt local ou un vaste centre de distribution, la sélection du système de stockage approprié peut avoir de grandes conséquences sur votre productivité, vos coûts et votre capacité à répondre aux demandes du marché.
Analyse des types de stockage de palettes et leurs caractéristiques techniques
Chaque système présente des avantages et des inconvénients en termes de capacité, d'accessibilité et d'efficacité opérationnelle.
Systèmes de rayonnages à palettes statiques : conception et capacité de charge
Les rayonnages à palettes statiques constituent la solution la plus courante et polyvalente pour le stockage de palette à Paris et dans d'autres grandes villes. Ces structures métalliques robustes donnent un accès direct à chaque palette, ce qui facilite la gestion des stocks et la préparation des commandes. La capacité de charge de ces systèmes varie généralement entre 1 000 et 4 000 kg par niveau, en fonction de la qualité des matériaux et de la conception. Les rayonnages statiques sont particulièrement adaptés aux entrepôts gérant un grand nombre de références avec un taux de rotation moyen à élevé. Ils permettent une organisation flexible de l'espace et s'adaptent facilement aux changements de configuration. Cependant, leur principal inconvénient est une utilisation de l'espace moins idéale que certains systèmes plus denses.
Solutions de stockage dynamique : FIFO et LIFO avec convoyeurs à rouleaux
Les systèmes de stockage dynamique utilisent la gravité pour déplacer les palettes le long de convoyeurs à rouleaux. Ils se déclinent en deux variantes principales : FIFO (First In, First Out) et LIFO (Last In, First Out). Ces solutions sont particulièrement efficaces pour gérer des produits à forte rotation ou avec des dates de péremption. Le système FIFO est idéal pour les produits frais ou datés, car il assure une rotation naturelle des stocks. Les palettes sont chargées d'un côté et se déplacent automatiquement vers l'autre extrémité pour le prélèvement. Le LIFO, quant à lui, est plus compact et convient aux espaces restreints, mais limite l'accès aux palettes les plus anciennes.
Stockage par accumulation : drive-in, drive-through et push-back
Les systèmes de stockage par accumulation permettent de maximiser la densité de stockage en sacrifiant une partie de l'accessibilité individuelle des palettes. Ces solutions sont particulièrement adaptées aux produits homogènes avec un faible nombre de références et un volume élevé par référence. Le drive-in et le drive-through permettent aux chariots élévateurs de pénétrer directement dans la structure de stockage pour déposer ou récupérer les palettes. La différence principale se trouve dans le fait que le drive-through donne un accès des deux côtés, facilitant la gestion FIFO, tandis que le drive-in ne dispose que d'une seule entrée. Le système push-back, quant à lui, utilise la gravité et des chariots sur rails pour densifier le stockage tout en maintenant un certain niveau d'accessibilité. Les palettes sont poussées vers l'arrière lors du chargement et reviennent automatiquement en façade lors du déchargement.
Systèmes automatisés : transstockeurs et navettes pour haute densité
Pour les entrepôts nécessitant une très haute densité de stockage et une bonne gestion des flux, les systèmes automatisés représentent l'évolution ultime des solutions de stockage de palettes. Ces technologies avancées sont particulièrement adaptées aux entrepôts géants où l'optimisation de chaque mètre carré est indispensable. Les transstockeurs sont des robots de manutention capables de circuler dans des allées très étroites et à des hauteurs impressionnantes, pouvant atteindre 40 mètres. Ils permettent une gestion entièrement automatisée des mouvements de palettes, réduisant ainsi les erreurs et améliorant les flux. Les systèmes de navettes, quant à eux, apportent une solution intermédiaire entre les systèmes manuels et les transstockeurs. Ces petits véhicules autonomes circulent dans les rayonnages pour déposer et récupérer les palettes, permettant une densité de stockage élevée tout en maintenant une certaine flexibilité.
Évaluation des contraintes logistiques et opérationnelles
Le choix d'une solution de stockage de palettes ne peut se faire sans une analyse approfondie des contraintes logistiques et opérationnelles spécifiques à votre activité. Cette évaluation permet de déterminer le système le plus adapté à vos besoins actuels et futurs.
Calcul du taux de rotation des stocks et impact sur le choix du système
Le taux de rotation des stocks est un indicateur pour déterminer le type de système de stockage le plus approprié. Un taux de rotation élevé nécessite généralement un accès rapide et fréquent aux palettes, favorisant ainsi les systèmes à accès direct comme les rayonnages statiques ou dynamiques.
Analyse des flux de marchandises : cross-docking vs stockage longue durée
La nature de vos flux de marchandises influence grandement le choix du système de stockage. Si votre activité implique beaucoup de cross-docking, où les marchandises transitent rapidement de la réception à l'expédition sans stockage prolongé, des solutions flexibles comme les rayonnages dynamiques ou même des zones de stockage au sol peuvent être préférables. En revanche, pour le stockage longue durée, des systèmes denses comme le stockage par accumulation ou les solutions automatisées peuvent améliorer l'optimisation de l'espace.
Gestion des références multiples : picking et préparation de commandes
La diversité de votre catalogue produits et la fréquence des opérations de picking ont des conséquences directes sur le choix du système de stockage. Pour les entrepôts gérant de nombreuses références avec des prélèvements fréquents, des solutions apportant un accès direct à chaque palette, comme les rayonnages statiques ou les systèmes dynamiques FIFO, sont souvent plus efficaces. Pour optimiser la préparation des commandes, considérez l'intégration de zones de picking dédiées au niveau du sol, avec des emplacements de réserve en hauteur. Cette configuration permet de réduire les déplacements et d'accélérer le processus de préparation.
Optimisation de l'espace de stockage et de la manutention
L'optimisation de l'espace de stockage est un enjeu majeur dans la conception d'un entrepôt efficace. Elle nécessite une réflexion approfondie sur l'utilisation verticale de l'espace, la rationalisation des allées et l'ergonomie des postes de travail.
Maximisation de la hauteur : racks grande hauteur et systèmes mezzanine
L'exploitation de la hauteur disponible est nécessaire pour maximiser la capacité de stockage. Les racks de stockage grande hauteur permettent de stocker des palettes jusqu'à 30 mètres de haut, multipliant ainsi la capacité de stockage sans augmenter l'empreinte au sol. Ces systèmes nécessitent cependant des équipements de manutention spécialisés, comme des chariots élévateurs à mât rétractable ou des transstockeurs. Les systèmes mezzanine apportent une alternative intéressante en créant des niveaux supplémentaires pour le stockage ou les opérations de picking. Ils sont particulièrement adaptés aux entrepôts gérant de nombreuses références de petite taille ou nécessitant des zones de préparation de commandes dédiées.
Rationalisation des allées : very narrow aisle (VNA) et rayonnages mobiles
La réduction de la largeur des allées est un moyen efficace d'augmenter la capacité de stockage. Les systèmes Very Narrow Aisle (VNA) permettent de réduire la largeur des allées à moins de 1,8 mètre, augmentant ainsi la densité de stockage par rapport aux configurations traditionnelles. Ces systèmes nécessitent des chariots élévateurs spécialisés capables d'opérer dans des espaces restreints. Les rayonnages mobiles représentent une solution encore plus radicale pour maximiser l'espace. Montés sur des rails, ces rayonnages peuvent être déplacés pour créer une allée d'accès uniquement là où c'est nécessaire. Cette configuration permet d'éliminer les allées fixes et d'augmenter considérablement la capacité de stockage, bien qu'au prix d'un accès moins rapide aux palettes.
Ergonomie et sécurité : normes EN 15635 et FEM 10.2.02 pour l'inspection des rayonnages
L'optimisation de l'espace ne doit pas se faire au détriment de la sécurité et de l'ergonomie. Les normes européennes EN 15635 et FEM 10.2.02 fournissent des directives nécessaires pour l'inspection et la maintenance des systèmes de rayonnages. Ces normes préconisent des inspections régulières pour détecter les dommages potentiels et maintenir l'intégrité structurelle des installations. L'utilisation de systèmes dynamiques ou de carrousels peut réduire considérablement les déplacements et les efforts physiques des opérateurs, améliorant ainsi la productivité et réduisant les risques de blessures.
Intégration technologique et gestion informatisée des stocks
L'intégration de technologies avancées dans la gestion des stocks est devenue incontournable pour optimiser les opérations de stockage et de manutention. Ces solutions permettent une visibilité en temps réel sur les stocks et facilitent la prise de décision.
Systèmes WMS (warehouse management system) pour l'optimisation des emplacements
Un système de gestion d'entrepôt (WMS) permet d'optimiser l'utilisation des emplacements de stockage. Ces logiciels sophistiqués analysent en temps réel les caractéristiques des produits, les flux de marchandises et les contraintes opérationnelles pour déterminer le meilleur emplacement pour chaque palette. Les WMS modernes intègrent des algorithmes d'optimisation qui peuvent prendre en compte de multiples éléments tels que :
La fréquence de picking des produits
Les compatibilités de stockage
Les dates de péremption
Les dimensions et poids des palettes
La capacité des équipements de manutention
Cette optimisation dynamique des emplacements peut augmenter l'efficacité des opérations de stockage et de préparation des commandes.
Technologies RFID et codes-barres pour la traçabilité des palettes
L'utilisation de technologies d'identification automatique comme les codes-barres et la RFID (Radio Frequency Identification) permet une traçabilité précise des palettes à travers l'entrepôt. Ces technologies facilitent les opérations de réception, de stockage et d'expédition en réduisant les erreurs manuelles et en accélérant les processus. La RFID, en particulier, apporte certains avantages pour la gestion des palettes :
Lecture à distance sans ligne de vue directe
Capacité à lire plusieurs étiquettes simultanément
Possibilité de stocker plus d'informations que les codes-barres traditionnels
Meilleure durabilité des étiquettes dans des environnements difficiles
Solutions IoT pour la surveillance en temps réel de l'occupation des emplacements
L'Internet des Objets (IoT) offre de nouvelles possibilités pour la surveillance en temps réel de l'occupation des emplacements de stockage. Des capteurs peuvent être installés sur les rayonnages pour détecter la présence ou l'absence de palettes, permettant ainsi une mise à jour automatique et instantanée de l'état des stocks. Ces solutions IoT peuvent également fournir des informations précieuses sur l'utilisation des emplacements de stockage au fil du temps, aidant ainsi à identifier les opportunités d'optimisation.
Analyse coût-bénéfice et retour sur investissement (ROI)
L'analyse coût-bénéfice et le calcul du retour sur investissement sont nécessaires pour choisir judicieusement une solution de stockage de palettes. Ces évaluations permettent de déterminer la rentabilité à long terme et l'efficacité opérationnelle des différentes options disponibles sur le marché.
Comparaison des coûts d'installation : systèmes conventionnels vs automatisés
Les systèmes de stockage conventionnels présentent généralement des coûts d'installation initiaux plus faibles, mais nécessitent davantage de main-d'oeuvre pour leur exploitation. À l'inverse, les solutions automatisées requièrent un investissement initial plus conséquent, compensé par une réduction des frais de personnel à long terme.
Évaluation des gains de productivité : réduction des temps de manutention
Les gains de productivité sont déterminants dans le choix d'une solution de stockage. Les systèmes automatisés permettent une réduction des temps de manutention, avec des performances pouvant atteindre jusqu'à 200 mouvements de palettes par heure, contre 20 à 30 pour un opérateur humain. Cette augmentation de la cadence se traduit par une amélioration globale de l'efficacité opérationnelle et une réduction des délais de traitement des commandes.
Calcul de la densité de stockage et optimisation de la surface au sol
La densité de stockage influence directement la rentabilité d'un système de stockage. Les solutions automatisées améliorent l'optimisation de l'espace vertical, permettant d'augmenter la capacité de stockage par rapport aux systèmes conventionnels. Cela se traduit par une réduction des coûts immobiliers et une meilleure utilisation des surfaces disponibles.